
Кроме этого, технология позволит отливать слитки из новых сплавов, то есть шагнуть вперед в производстве готовых изделий из алюминия.
Лекарство для алюминия
Открыть собственную компанию Евгений Павлов решил в 2010-м году. К этому моменту за плечами были аспирантура по электротехнологиям и работа в научно-производственном Центре магнитной гидродинамики, где он занимался созданием оборудования для металлургических производств под руководством доктора наук Виктора Тимофеева.
В 2011 году в ходе научных исследований в СФУ, где Павлов параллельно работал преподавателем, возникла идея, ставшая основой для дальнейшего бизнеса и научных исследований. Она отвечала главному критерию — новизне, и была актуальна не только для отечественного, но и для мирового рынка. Идея была нацелена на решение масштабной технологической задачи металлургической отрасли — устранению дефектов в алюминиевых слитках, качество которых в значительной степени определяют свойства и качество конечной продукции.
— После тщательной проработки и оценки идеи мы решили продвигать ее на мировом рынке: увидели, что она способна решить комплекс проблем, которые есть у каждого крупного производителя алюминия и изделий из него. Представьте, что вы варите суп: сложили в кастрюлю все необходимые ингредиенты, но не перемешали их. Вряд ли суп получится вкусным, если компоненты не распределить по кастрюле. Что-то подобное происходит и при литье габаритных алюминиевых слитков. Из-за того, что в сплаве присутствуют компоненты различной плотности с разной температурой плавления, внутри они распределяются неравномерно. По этой причине появляются дефекты — трещины, пористость. Исключить их существующие технологии не позволяют. Наша же разработка выравнивает состав и температуру при застывании, лишая конечный продукт дефектов.
Павлов поясняет: эта проблема актуальна для алюминиевой отрасли всего мира — а разработка красноярцев значительно снизит процент брака или устранит его вовсе. Но более самих алюминщиков в решении задачи заинтересованы производители деталей для автомобильной, судостроительной и авиационной отраслей. Ведь дефекты слитка неизбежно приводят к тому, что и конечная продукция, полученная из таких алюминиевых сплавов, будет некачественной. Именно так произошло с AirBus 380: из-за дефекта слитка на крыльях самолета образовывались трещины, отваливался кожух двигателя. Как следствие, производитель лайнера был вынужден отвечать за брак и терпел миллиардные убытки.
— Поэтому мы обратились к ведущему европейскому производителю деталей для AirBus с предложением устранить с помощью нашей технологии подобные дефекты. При этом договорились, что наше оборудование будет оплачено только в случае положительных результатов испытаний. Так началась дорогостоящая рискованная работа по созданию новой технологии за счет собственных средств.
Как продать изобретение
От идеи до воплощения проекта — производства и тестирования оборудования — прошло почти четыре года. Это время ушло на анализ рынка, математическое моделирование, отработку различных вариантов технологии, производство и испытания оборудования — команду проекта полностью устроил лишь третий по счету вариант. Ключевая задача — сделать эффективное, но в то же время дешевое в производстве и простое в использовании оборудование.
«Сделать дорого и сложно смогут многие, а вот недорого и просто — это задача, над которой нужно долго и упорно работать. И тут не обойтись без грамотного ученого, понимающего суть процессов, и без инженера, который придумает оптимальное техническое решение», — говорит Евгений Павлов.
Параллельно с работой над технологией, Евгений с командой своей компании «УниМет» занимался выстраиванием бизнес-процессов. Для выхода на международный рынок была создана компания Altek-MHD ltd (ее соучредителями являются СФУ и английская компания Altek Europe ltd). Одной из самых сложных бизнес-задач стал поиск площадки для тестирования технологии и оборудования.
— Вы сделали штуку, которая всем нравится и решает какую-то задачу, но это только первый этап. Изобретение нужно суметь продать, иначе это не инновационный бизнес, а инновационное творчество. Между этими понятиями огромная разница. А прежде чем продать инновацию, нужно доказать, что она работает — это испытания. В такой консервативной сфере как металлургия, где производственный процесс регламентирован и расписан на год вперед, сделать это совсем не просто.
Площадкой для испытания технологии стал завод в Швейцарии, на нем отливаются алюминиевые слитки, из которых завод выпускает свой конечный продукт — продукцию для авиа- и машиностроения. Условия, на которых удалось договориться со швейцарцами, Евгений Павлов называет «жесткими».
— Разработка технологии, производство оборудования и его установка в работающие на предприятиях литейные машины — все это мы делали за свои деньги. Договорились так: если технология доказывает свою эффективность, завод за нее платит, если нет — то нет. Жесткие условия, но для нас единственный вариант. Мы прекрасно понимали: ни один производитель не рискнет тратить полмиллиона евро на инновацию, которая еще не подтвердила свою эффективность на практике.
Испытания технологии заняли полгода — с апреля по октябрь 2015-го. Отлитые слитки распиливали, проводили рентгеноструктурный анализ каждого среза. Накопленная за полгода статистика подтвердила: разработанная красноярцами технология работает — слитки однородны по своему составу, в них нет трещин и пористости. Кроме этого, скорость литья с использованием технологии увеличивается до 80%: благодаря электромагнитному перемешиванию сплав кристаллизуется быстрее.
Швейцарский завод-производитель, как это и было прописано в договоре, приобрел у красноярцев технологию и оборудование.
В свою очередь разработчики технологии, имея на руках фактические результаты, начали выводить свое детище на мировой рынок.
Контракты на миллионы
Сейчас инноваторы патентуют технологию в России, США, Китае и Европе. После этого начнется работа с непосредственными заказчиками. Интерес к разработке уже проявили более десятка зарубежных компаний-производителей алюминия. В их числе Alcoa, Chalco, Hydro, BHP Billiton, Dubal и другие. Ожидается, что среди отечественных производителей одними из первых возможности технологии будут использовать РУСАЛ и Каменск-Уральский металлургический завод (ОАО «КУМЗ»). И список этот продолжает пополняться.
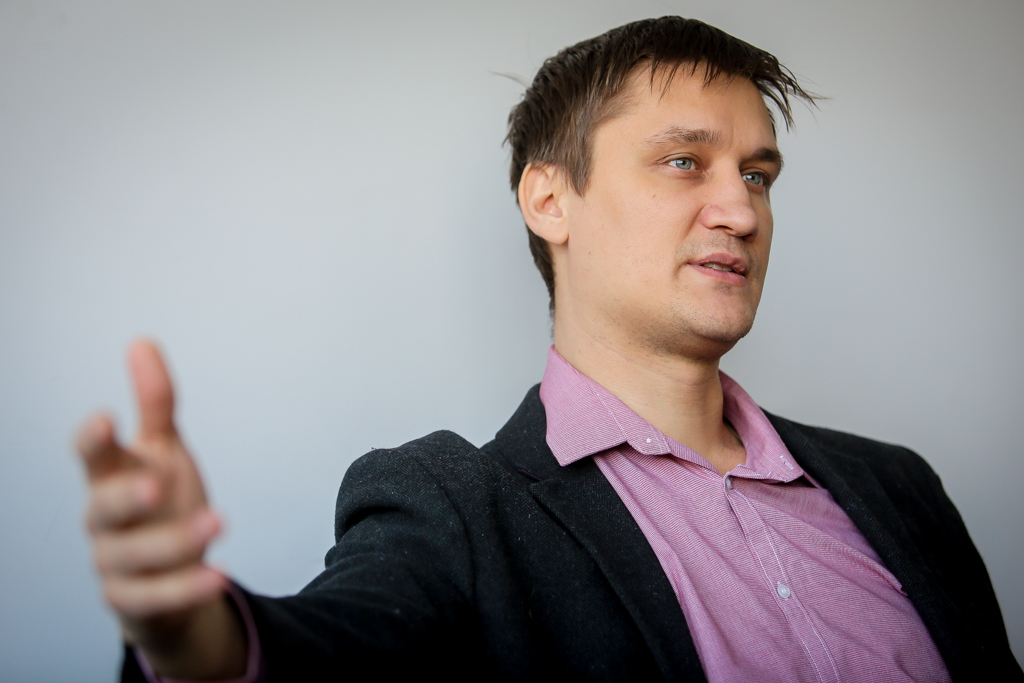
Суммарный экономический эффект применения технологии — до 3 млн евро в год на одну литейную установку, при общей стоимости оборудования 750 тыс. евро. Говоря проще, вложения окупают себя за три месяца. При этом оборудование устанавливается на уже работающие литейные установки, что особенно важно для крупных производств. Однако, подводя промежуточные итоги работы над проектом, Павлов оперирует не только цифрами.
— Наша технология — это серьезный шаг и новые возможности для алюминиевой промышленности. К примеру, прочность традиционного авиационного сплава AA7071 500 МПа примерно как у стали. Но она может быть и больше — 700 МПа, 1000 МПа, для этого в сплав нужно добавить составляющие, скажем, больший процент цинка — до 11 %, нано-частицы. Раньше это бы автоматически привело к дефекту слитка из-за расслоения компонентов. Наша технология позволяет выравнивать химический состав, а, значит, расширяет поле работы над новыми сплавами и изделиями из них.
Что такое более прочный алюминий? Это уменьшение массы автомобильных кузовов, деталей самолетов, то есть, экономия на топливе. Это огромный экономический эффект, причем не точечный, а глобальный.
Это также и возможность придавать новые свойства металлам — яркий пример того, как научный подход к металлургии решает существующие проблемы и открывает новые горизонты.
Наталья Мороз, интернет-газета Newslab.ru